There are many kind of rubber moding way, include injection molding, liquid injection molding, insert molding, compression molding and blow molding. These methods have their advantage and disadvantage; however, injection molding is used more widely than any other method. There is also a more economic rubber molding in general is rubber extrusion.
Injection Molding
The first step in the injection molding process involves collecting raw rubber material, then the raw material is placed into a hopper that is suspended over a conveyance channel. Then the material is then released, and processed through a channel that features a large turning screw. By the time the material reaches the end of the channel, it is completely melted as a result of a combination of the heating elements within the channel, and the friction caused by the screw’s motion. At the end of the channel is a mold cavity into which the molten rubber is injected. The elements of heat and pressure work together to ensure that the molten rubber fills the cavity entirely, down to the very contours of the mold, and is uniformly distributed. The molten rubber is allowed to cool and harden within the mold, and can be safely removed from the mold cavity once it reaches a solid state.
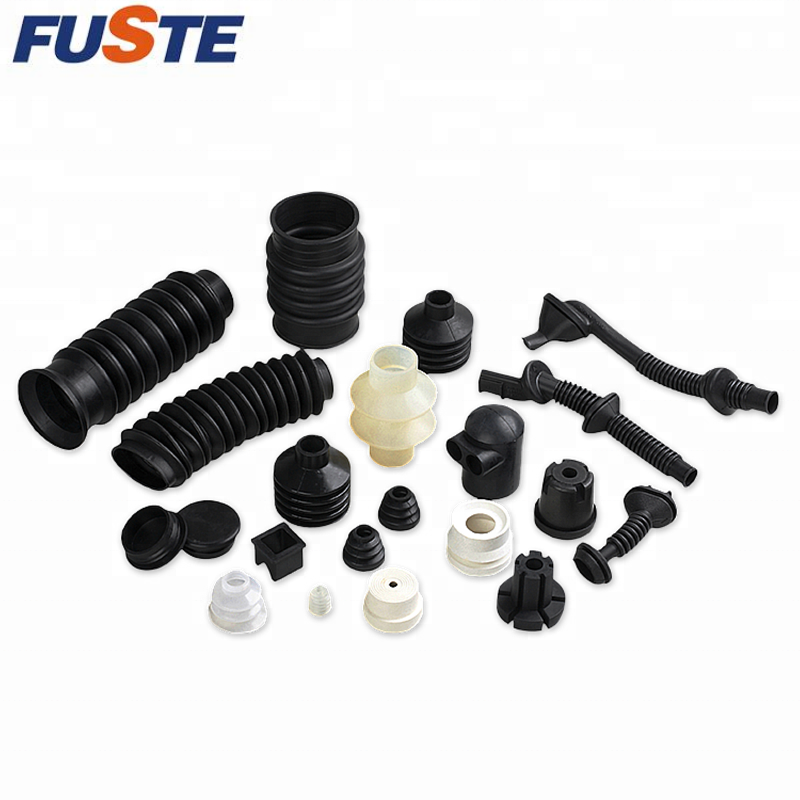
Liquid Injection Molding
Liquid silicone rubber (LSR) is a two-part silicone-based polymer joined together by a chemical bond. It’s most commonly used to create injection molded parts for products used in industries such as automotive, food, appliances, textiles, and consumer goods.
When the polymer is injection molded and heated, the catalyst initiates a cross-linking progression. This progression gives the substance permanent strength and shape after the curing process.
The resulting material is strong and durable, making it ideal for a variety of products including:
Baby feeding product
Appliance hardware
Automotive parts
Electronics interfaces
O-rings
Insert Molding
Insert molding is a type of rubber and plastic injection molding. During insert molding, manufacturers mold or form rubber parts around non-rubber parts, called inserts. Common insert products include baby spoon and silicone baby bottle
Compression Molding
Compression molded parts are made when the factory pre-weigh, pre-measure ,mixthing the raw material, and then inserts it into a pre-shaped mold cavity. After that, they close the mold, compressing and squeezing the stock with high tempreture until it melt and takes on the shape of the mold. Then, they are vulcanized to harden before removing the mold. The compression molding process is often up removing the burrs, Through rubber compression molding, manufacturers can make large, complex products quite inexpensively.
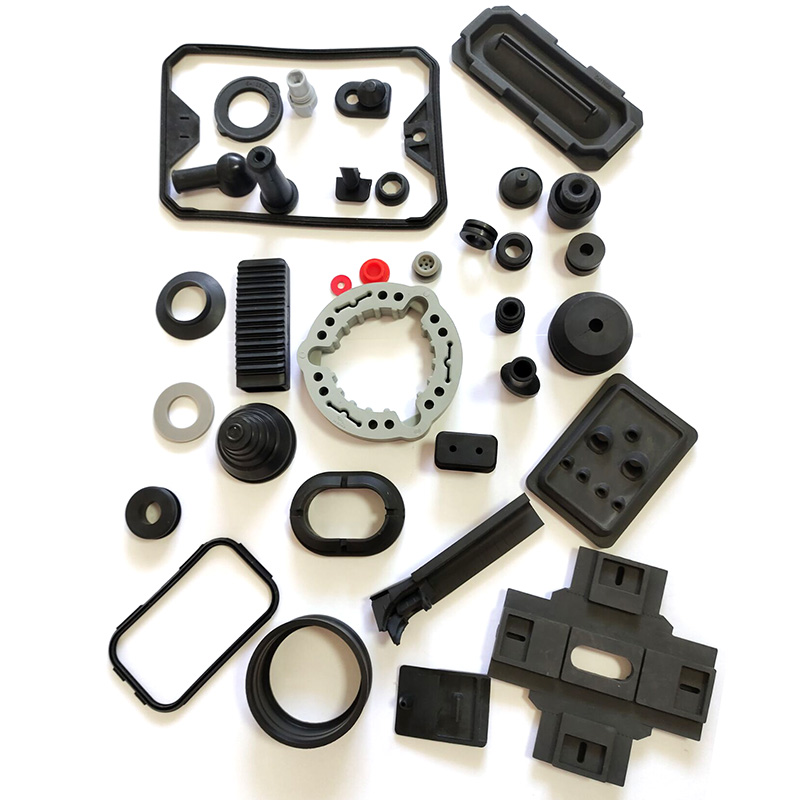
Blow Molding
Rubber blow molding is a molding process by which hollow rubber products are formed. To expand the part, manufacturers clamp the parison to a mold and then blow compressed air into the parison hole. As the rubber expands, it touches the mold and takes on its shape. After it cools and hardens, manufacturers open the mold and take out the newly formed part.
Rubber Extrusion
Rubber parts can alternatively be produced through rubber extrusion. However, extruding machines have much more limited capabilities. An extruder only has control over the X and Y axes, and are thus much more suited for the production of simpler rubber products such as rubber profile or rubber sheets. Rubber molding allows from design control over three axes due to the process involving a molding cavity instead of a die.
Advantages of Injection molding
· Fast production.
· Minimum wastage of material.
· Design flexibility.
· Labor cost is low.
· Flexibility in color and material.
benefits of using liquid silicone rubber
1. Superior heat stability
LSRs can withstand temperatures up to 180 °C with no melting or creeping. They have become a popular option for heavy-duty and automotive applications like seals and gaskets.
2. Low-temperature flexibility
Thermoplastic elastomers can lose their flexibility at extreme temperatures. At low temperatures, they become harder and more brittle until they eventually crack. LSRs, however, remain flexible at temperatures as low as -50 °C. They are an excellent choice for any products that need to operate in a low-temperature environment.
3. Aging resistance
Aging resistance is an important factor in determining the right material for your injection molding process. Cured LSR materials provide excellent resistance to UV rays, weathering, and aging. They are ideal for use in applications where long-term exposure to the elements is a concern.
4. Chemical resistance
Thermoplastic elastomers can resist chemicals in a broad range of applications. But they only offer chemical resistance in moderate temperature ranges. LSR offers low water absorption and excellent resistance to common chemicals even when exposed to extreme temperatures.
5. Low compression set
A low compression set means that materials can resist permanent deformation under a constant strain. LSRs have a very low compression set, typically in the range of 15%-20%. They are able to retain their elasticity even when compressed for extended periods of time and subjected to different temperature ranges.
6. Great shelf life reliability
The shelf life of liquid silicone rubber is one of the key factors contributing to the ease of use in a manufacturing environment. Most LSR products are available with a shelf life of at least one year.
7. Electrical resistance
Electronics manufacturers need to know that the materials they are using can resist corona discharge. LSR offers high resistance to electrical stress without impacting the conductivity of the final product. For this reason, these materials are commonly used in high-voltage applications and electrical parts.
Choosing a Manufacturer
When selecting a rubber molding service supplier, you need consider the following: What’s my application? What qualities must my molded product have (tensile strength, corrosion resistance, flexibility, temperature resistance, etc.? Do I need to adhere to any industry/regional standard requirements? How much customization do I require? How many items do I need? What’s my budget? What’s my timeline?
By knowing the answers to these questions, you can know what product and service offerings to look for when researching, and have a more productive conversation with your manufacturers. We know that there are a lot of manufacturers and suppliers floating around out there, some of dubious quality. So if chose us we can provide you the solution how to chose the material according to your request , like if oil resistance , can use the NBR or NBR +PVC materil , if water-proof and Ozone resistance, sunproof , you can chose the EPDM material . For the custom items , we can provide our professional suggestion to make the drawing to be reality .
Welcome to contact us ! sales2@fuste.com.cn